Tolerance vs. Fit & Function
With 40 years of experience, we rely on industry experience over industry standards to maximize the quality of your end-product.
In the plastic extrusion industry, length tolerances can vary based on factors such as material properties, profile design, and cutting methods. A typical length tolerance for extrusions is ±1/16 inch. For longer lengths, the tolerance may increase proportionally. Jifram Extrusions emphasizes the importance of balancing tight tolerances with cost-effectiveness. Overly stringent tolerances can lead to increased tooling costs, longer setup times, and higher scrap rates. Their engineers collaborate with clients to determine optimal tolerances that ensure both fit and functionality while minimizing costs. For precise applications, Jifram offers cutting services that can achieve tighter length tolerances, though this may add to the overall cost. Engaging with their engineering team early in the design process can help set realistic tolerance expectations tailored to your project’s requirements.
Thanks to the technological advancements made in measurement, extrusion equipment, tooling, and thermodynamic materials, tolerances are able to get a lot tighter. But that doesn’t always mean they’re more accurate. In fact, tolerances that are over-engineered are one of the major contributing factors in cost escalation due to the higher tooling costs, longer startup times, repeat runs, and more scrap generation. Industry-standard tolerance tables exist as a guide, but as plastic extruders, we want to achieve optimal tolerance to ensure the fit and functionality of your end-product and even save you money in the long run.
Jifram’s engineers rely on expertise and experience to help our customers consider the critical aspects of each profile. How tight the tolerance depends on the intended use, as well as consideration for materials, mating parts, dimensional stacking, and overall manufacturability and production. For example, we may need to reduce overall output in order to maintain better control over the cooling process to ensure a precise fit.
It’s crucial to begin the collaboration process with an engineer early on in the process in order to set tolerance expectations based on your project requirements. At Jifram, we spend time with designers to define precise extrusion tolerances based on all of the above critical factors, rather than immediately revert to defaults, over-engineer tolerances, or put too much emphasis on non-critical dimensions – all of which can contribute to a poor profile fit, as well as poor function, at a detrimental cost.
Our expert engineers can tackle anything.
If you have questions or concerns about your design, and you aren’t sure what tolerances are critical, achievable, or cost-effective, our extrusion experts are here to help you and ensure the success of your project.
Some helpful design hints from our engineers.
To prepare for a conversation with an extrusion engineer and ensure a successful design, it’s important to consider several factors in the beginning phases of your design process. Look for these opportunities to improve your cost:
- Limit the complexity of profile design.
- Make sure wall variation and thickness is consistent, especially in the cross-sectional areas.
- Rely on standard shapes/profiles when possible.
- Choose optimal raw materials.
- Allow for optimal process/environmental conditions during the life of production.
- Indicate which areas of your design are not critical, such as surface appearance.
- All of the above can also help avoid the use of costly secondary operations.
After the basic design is determined, our engineers can review your concept and suggest additional ideas to maximize processability, dimensional control, and part performance, as well as decrease tooling costs, reduce production efficiencies, and avoid bowing and twisting of the parts. Prior to the production run, we also request the mating part so that as parts come off the line, we can ensure they fit and function as expected.
Again, if you have questions or concerns about your design, set up a conversation with one of our extrusion experts right away. We bring over 40 years of plastic extrusion experience to your project. We’re here to help!
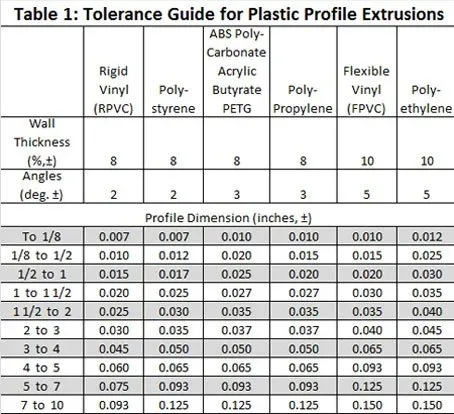
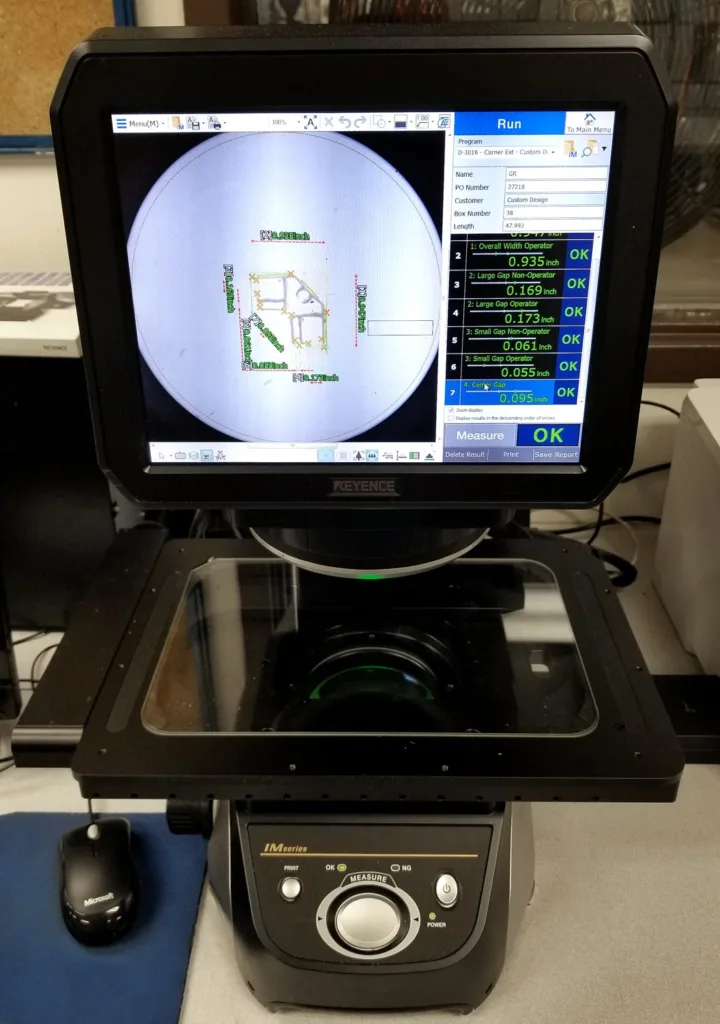
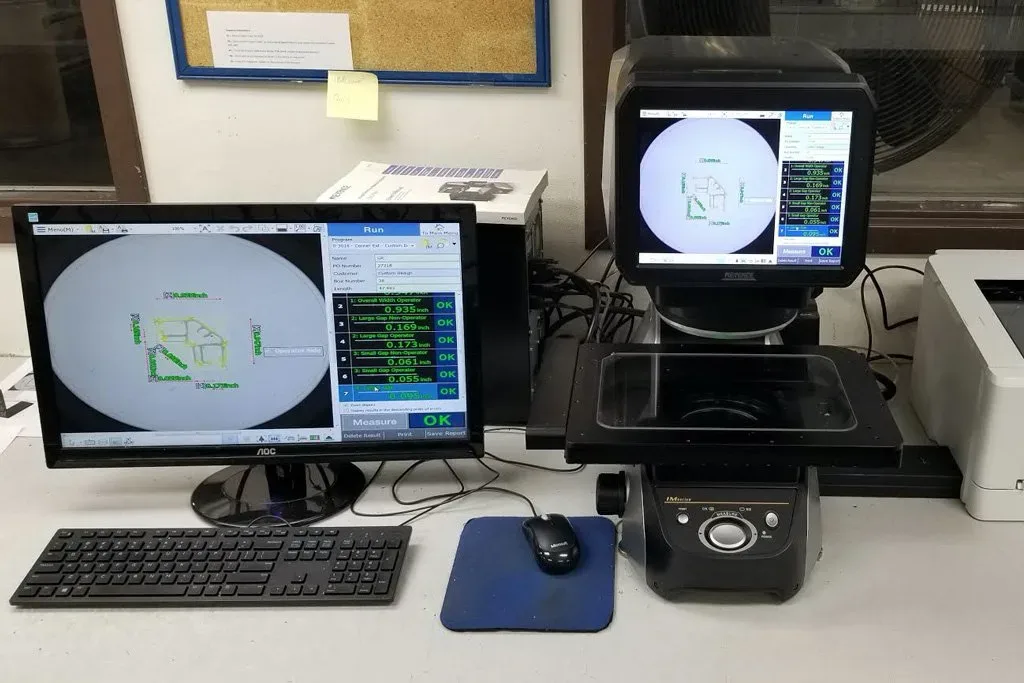